در فرایند تولید محصولات پلیمری از مستربچ افزودنی برای بهبود ویژگی های مکانیکی و ظاهری محصولات از مستربچ افزودنی استفاده می شود. مستربچ افزودنی به شکل گرانول با غلظت بالا تولید می شود و در اندازه مشخصی به مواد پلیمری اضافه می شود. از دلایل محبوبیت و استفاده زیاد از مستربچ افزودنی می توان به توزیع یکنواخت در مواد پلیمری، بهبود کیفیت محصولات، کاهش هزینه ها، افزایش بهره وری در فرایند تولید، سازگاری با محیط زیست و .. اشاره کرد.برخی از مستربچهای افزودنی میتوانند نقش مهمی در کاهش مصرف پلاستیک، بهبود قابلیت بازیافت و افزایش طول عمر محصولات پلاستیکی ایفا کنند. استفاده از مستربچ باعث کاهش مصرف مستقیم افزودنیهای خالص و بهینهسازی مصرف مواد اولیه میشود، که در نتیجه هزینههای تولید را کاهش میدهد. از انواع مستربچ افزودنی می توان به ضد مه، لیز کننده، آنتی یووی، آنتی بلاک، کمک فرایند، براق کننده، شفاف کننده، آنتی استاتیک، آنتی اکسیدان و.. اشاره کرد. به دلیل مزایای گسترده مستربچهای افزودنی، این مواد در صنایع مختلفی مانند بستهبندی، خودروسازی، لوازم خانگی، پزشکی و صنایع الکترونیکی بسیار مورد استفاده قرار میگیرند. به دلیل تنوع بالای نیازها و کاربردهای پلاستیک، مستربچهای افزودنی نیز با فرمولاسیونهای متنوعی تولید میشوند. این مستربچها علاوه بر بهبود کیفیت و عملکرد محصولات، باعث بهینهسازی فرآیند تولید، افزایش دوام و کاهش هزینهها در صنایع مختلف میشوند. اضافه کردن افزودنیها به صورت مستربچ به جای استفاده از مواد خام به صورت جداگانه، هزینههای تولید را کاهش میدهد. مستربچها امکان کنترل دقیقتر و یکنواختی بهتر در خصوصیات نهایی محصولات را فراهم میکنند. استفاده از مستربچها میتواند زمان تولید را کاهش داده و بازدهی فرآیند تولید را افزایش دهد.
مستربچ افزودنی چیست؟
دلایل تنوع بالای مستربچ افزودنی
مستربچ افزودنی به دلیل عوامل متعدد از جمله نیاز های مختلف صنایع پلاستیک در تولید محصولات پلیمری در انواع مختلفی تولید می شود. از عوامل مختلف تولید انواع مستربچ افزودنی می توان به کاربرد های مختلف آن در صنایع گوناگون، ویژگی های فنی و مکانیکی مورد نیاز محصولات مختلف، عملکرد های مختلف مستربچ، تفاوت در ترکیب مواد اولیه و پایه های پلیمری و .. اشاره کرد. مستربچ افزودنی بر اساس عملکرد به دسته بندی های مختلف از جمله: محافظت در برابر اشعه فرا بنفش، جلوگیری از رشد میکروب ها، افزایش عمر محصولات، کاهش جذب گرد و غبار، کاهش اصطکاک در فیلم های پلاستیکی و.. اشاره کرد. از آنجایی که ترکیب مستربچ باید با نوع پلیمر و فرایند تولید همخوانی داشته باشد تفاوت در ترکیب مواد اولیه و پایه های پلیمری سبب ایجاد تنوع در تولید مستربچ افزودنی می شود. برای مثال برخی از محصولات پلیمری در محیط های مرطوب استفاده می شوند و باید در فرایند تولید آن ها از مستربچ افزودنی آنتی باکتریال و مقاوم به رطوبت استفاده شود.در صنایع غذایی از مستربچ های که با توجه به رعایت استاندارد های بهداشتی ساخته می شوند استفاده می شود.
مستربچ لیز کننده و ویژگی های استفاده از آن
یکی از چالش هایی که تولید کنندگان در روند ساخت محصولات پلاستیکی با آن رو به رو هستند می توان به چسبیدن مواد اولیه به بدنه دستگاه های تولید اشاره کرد. بدون شک جلوگیری از چسبیدن مواد پلیمری به بدنه دستگاه ها باعث کاهش هزینه های تمیز کاری و هدر رفت مواد اولیه خواهد شد. برای کاهش هزینه های تولید محصولات پلاستیکی از افزودنی شتاب دهنده های فرایند لیز کننده استفاده خواهد شد. در واقع این مستربچ به لیز شدن مواد اولیه و عدم چسبندگی مواد به دستگاه کمک بسیاری می کند. مستربچ لیز کننده از اصطکاک بین سطوح پلاستیکی کاهش می دهد. یکی از مزایای استفاده از مستربچ لیز کننده بهبود فرایند تولید محصولات پلیمری می باشد. چرا که با استفاده از این مستربچ لاه های پلاستیکی کمتر به یک دیگر می چسبند. یکی از نقاط مثبت مستربچ لیز کننده افزایش دوام و طول عمر محصولات پلاستیکی نیز می باشد. چرا که مواد پلیمری با استفاده از مستربچ لیز کننده کمتر دچار سایش خواهند شد.معمولا برای تولید فیلم های پلاستیکی مانند بسته بندی های پلی اتیلنی، پلی پروپلین و قطعات تزریقی پلاستیکی با سطح صاف، تولید نخ های مصنوعی و الیاف پلاستیکی، صنعت خودروسازی و .. از مستربچ لیز کننده استفاده می شود. سایر مزایای استفاده از مستربچ لیز کننده عبارتند از :
- جدا شدن راحتتر محصولات پلیمری: مانند کیسههای پلاستیکی که به راحتی از هم جدا میشوند.
- افزایش مقاومت در برابر سایش: سطح محصول را صافتر کرده و باعث بهبود خواص مکانیکی آن میشود.
بهبود خاصیت روانکاری داخلی: در برخی کاربردها باعث کاهش نیاز به روغنهای روانکننده اضافی میشود. - بهبود فرآیند تولید: در تولید فیلمهای پلاستیکی مانند PE و PP، باعث افزایش سرعت تولید و کاهش مشکلاتی مانند چسبیدن فیلمها به هم میشود.
نکات مهم در انتخاب مستربچ لیز کننده با کیفیت
امروزه تولید کنندگان بسیاری در زمینه تولید مستربچ فعالیت می کنند بنابراین بهتر است از تولید کنندگان معتبر خرید خود را انجام دهید. از نکات مهم در خرید مستربچ افزودنی لیز کننده می توان به میزان کاهش اصطکاک در محصول اشاره کرد. چرا که برخی از مستربچ های لیز کننده اثر دائمی دارند اما سایر مدل های دیگر به مرور زمان تجزیه شده و خاصیت خود را از دست می دهند. مستربچ لیز کننده باید با پلیمر پایه محصول شما (مانند PE، PP، PET، PVC و…) سازگاری داشته باشد تا عملکرد بهینهای ارائه دهد. مستربچ لیز کننده در دو نوع داخلی و خارجی تولید شده که باید نسبت به نیاز خود افزودنی مود نیاز را خریداری کنید. در خرید مستربچ لیز کننده با کیفیت باید به میزان دوام و پایداری حرارتی آن توجه ویژه ای داشته باشید. اگر افزودنی لیز کننده مقاومت کافی در دما های بالای را نداشته باشد دچار تغییر رنگ و تجزیه مواد می شود. بدون شک خرید مستربچ با کیفیت سبب کاهش مصرف انرژی و افزایش سرعت تولید محصولات پلیمری می شود.
مستربچ آنتی یو وی
در تولید محصولات پلیمری برای افزایش مقاومت آن ها در برابر اشعه ماورا بنفش از مستربچ آنتی یووی استفاده می شود. از مزایای ترکیب مواد پایه پلیمری با مستربچ آنتی یووی می توان به افزایش طول عمر محصول، حفظ خواص مکانیکی، جلوگیری از تغییر رنگ و زرد شدن پلاستیک، و کاهش اثرات مخرب تابش نور خورشید اشاره کرد.از مهم ترین کاربرد های مستربچ آنتی یو وی می توان به تولید فیلم های کشاورزی، لوله و اتصالات پلیمری، قطعات خودرویی، تولید مصالح ساختمانی و دکوراسیون داخلی، الیاف و نخ های مصنوعی و .. اشاره کرد. از ویژگی های تولید محصولات پلاستیکی با استفاده از مستربچ آنتی یو وی می توان به افزایش طول عمر محصولات، کاهش هزینه های تعمیرات و نگهداری محصولات پلیمری، جلوگیری از شکنندگی، تغییر رنگ و .. اشاره کرد.
حاوی مواد مقاومکننده به اشعه فرابنفش برای جلوگیری از تخریب پلیمرها در مقابل نور خورشید است. مستربچ مقاوم به یو وی به طور خاص برای محافظت از محصولات پلیمری در برابر اشعه ماورا بنفش طراحی شده است. در صنایع مختلف برای تولید محصولات متنوع پلیمری از جمله تولید لوازم پلاستیکی، بسته بندی، مبلمان و .. از افزودنی مقاوم به یو وی استفاده می شود. محصولات پلیمری که در فضای باز قرار می گیرند در معرض اشعه های مضر و تغییر رنگ یا زرد شدن هستند. در جهت افزایش کیفیت مصالح ساختمانی از این افزودنی استفاده می شود. برای مثال در ساختمان سازی کابل ها برق در معرض نور خورشید هستند. از ویژگی های استفاده از مستربچ مقاوم به یو وی می توان به افزایش عمر مفید محصولات، حفظ رنگ و ظاهر اولیه، مقاومت در برابر خوردگی و کاهش هزینه های نگهداری اشاره کرد. مهم ترین کاربر های مستربچ آنتی یو وی عبارتند از:
تولید قطعات خودرو : برای جلوگیری از تغییر رنگ و شکنندگی قطعات پلاستیکی داخلی خودرو از افزودنی آنتی یو وی در تولید آن ها استفاده می شود. دستگیره و کنسول خودرو در معرض تابش نور مستقیم خورشید هستند به همین ترتیب برای تولید آن ها از افزودنی آنتی یو وی استفاده می شود. از جمله قطعات بیرونی خودرو که با استفاده از مستربچ افزودنی آنتی یو وی تولید می شوند می توان به چراغ های خودرو اشاره کرد. سقف و پانل های بیرونی، روکش و پوشش ها و قطعات پلاستیکی نمای بیرونی خودرو با استفاده از این مستربچ تولید می شوند.
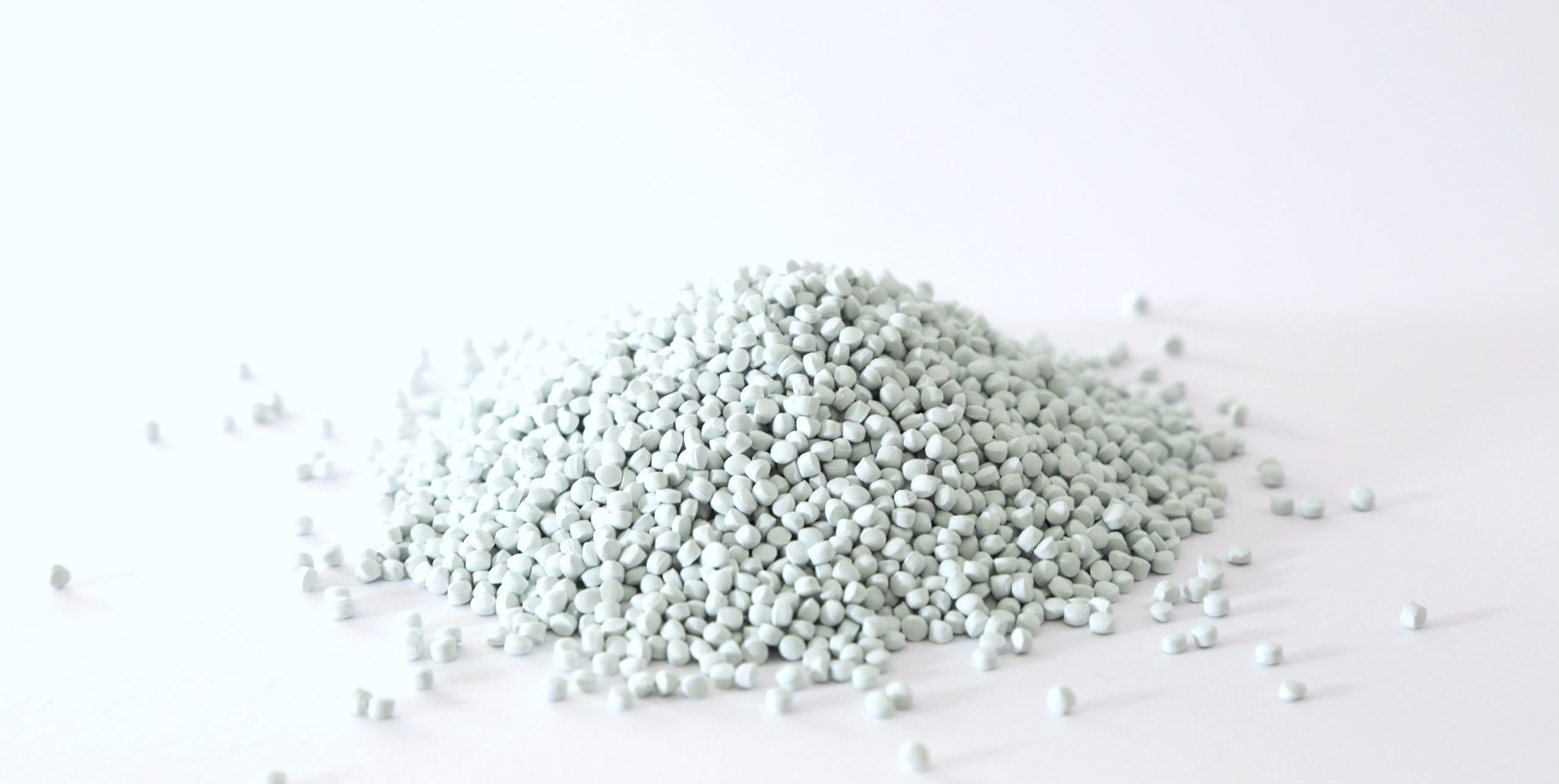
مستربچ آنتی اکسیدان
ترکیب مواد پایه پلیمری با مستربچ افزودنی آنتی اکسیدانت سبب تخریب زود هنگام پلیمر ها در محیط های گرم و در تماس با اکسیژن می شود. از ویژگی های افزودنی آنتی اکسیدان می توان به جلوگیری از تجزیه حرارتی و تخریب زود رس پلیمر ها اشاره کرد. مواد پلیمری در ترکیب با مستربچ افزودنی انتی اکسیدانت طول عمر بیشتری در شرایط محیطی مختلف پیدا خواهند کرد.حفظ براقیت و خواص مکانیکی محصولات پلاستیکی بسیار اهمیت دارد. به همین منظور در تولید محصولات پلاستیکی از افزودنی آنتی اکسیدان استفاده می شود. یکی از دیگر مزایای مستربچ افزودنی آنتی اکسیدان افزایش مقاومت مواد پلیمری در دمای بالا و جلوگیری از تخریب پلیمر نیز می باشد. همچنین با هدف های افزایش سفتی و استحکام مواد پلیمری و انعطاف پذیری بیشتر نیز می توان از مستربچ های آنتی اکسیدان استفاده کرد.مواد پلیمری در ترکیب با آنتی اکسیدان فرایند پذیری بهتری به دلیل عدم ایجاد رسوبات و تغییرات شیمیایی پیدا می کنند. مواد پلیمری بدون ترکیب با مستربچ افزودنی به مرور زمان دچار تغییر رنگ (زرد شدن) می شود.از کاربرد های مستربچ آنتی اکسیدان می توان به تولید فیلم های پلاستیکی و ظروف بسته بندی محصولات دارویی و غذایی در صنایع بسته بندی اشاره کرد. در تولید قطعات پلاستیکی خودرو که در معرض گرما و اکسیژن هستند به دلیل عدم تغییر رنگ از مستربچ آنتی اکسیدان استفاده می شود. در تولید لوله های پلاستیکی از جمله: لوله های پلی اتیلن و پلی پروپلین از افزودنی آنتی اکسیدان استفاده می شود.
مستربچ آنتی استاتیک
در تولید محصولات پلاستیکی توانایی جذب الکتریسیته ساکن توسط مواد پلیمری مشکل ساز خواهد بود. بنابراین برای کاهش جذب الکتریسیته ساکن توسط مواد پلیمری از مستربچ افزودنی آنتی استاتیک استفاده می شود. با استفاده از مستربچ آنتی استاتیک دیگر شاهد بروز مشکلات در تولید فیلم و قطعات پلاستیک نخواهید بود. از ویژگی های منحصر به فرد مستربچ آنتی استاتیک می توان به کاهش الکتریسیته ساکن برای جلوگیری از جذب گرد و غبار و ایجاد جرقه الکتریکی اشاه کرد. فرایند تولید محصولات پلیمری با استفاده از آنتی استاتیک به دلیل کاهش چسبندگی بسیار بهبود پیدا می کند. از کاربرد های مستربچ آنتی استاتیک در صنایع پلاستیک می توان به تولید الیاف و منسوجات مصنوعی، تولید قطعات خودرو، تولید بسته بندی های پلیمری مواد غذایی و .. اشاره کرد.
مستربچ ضد مه
یکی از افزودنیهای پرکاربرد در صنایع پلاستیک، بهویژه در بستهبندیهای غذایی و کشاورزی است. این افزودنی به کاهش یا حذف تشکیل قطرات آب (مه) بر روی سطح فیلمهای پلاستیکی کمک میکند. از مهم ترین دلایل استفاده از مستربچ افزودنی ضد مه در صنایع پلاستیک می توان به افزایش شفافیت و دید بهتر، افزایش کیفیت و ماندگاری محصولات غذایی، بهبود عملکرد گلخانه ای و افزایش رشد گیاهان و .. اشاره کرد. استفاده از مستربچ ضد مه در صنایع بستهبندی و کشاورزی نهتنها باعث بهبود کیفیت و عملکرد محصولات میشود، بلکه به کاهش ضایعات، افزایش ماندگاری محصولات و بهبود بهرهوری تولید کمک میکند. در تولید فیلمهای پلاستیکی، تجمع رطوبت در سطح فیلم میتواند باعث مشکلاتی در فرآیند لمینیت، چاپ یا دوخت حرارتی شود. استفاده از مستربچ ضد مه باعث بهبود عملکرد این فرآیندها میشود. قطرات آب روی بستهبندی میتوانند رشد باکتریها و کپکها را تسریع کنند. این افزودنی با کاهش تجمع رطوبت، ماندگاری مواد غذایی را افزایش میدهد.
مستربچ مقاوم به UV
حاوی مواد مقاومکننده به اشعه فرابنفش برای جلوگیری از تخریب پلیمرها در مقابل نور خورشید است. مستربچ مقاوم به یو وی به طور خاص برای محافظت از محصولات پلیمری در برابر اشعه ماورا بنفش طراحی شده است. در صنایع مختلف برای تولید محصولات متنوع پلیمری از جمله تولید لوازم پلاستیکی، بسته بندی، مبلمان و .. از افزودنی مقاوم به یو وی استفاده می شود. محصولات پلیمری که در فضای باز قرار می گیرند در معرض اشعه های مضر و تغییر رنگ یا زرد شدن هستند. در جهت افزایش کیفیت مصالح ساختمانی از این افزودنی استفاده می شود. برای مثال در ساختمان سازی کابل ها برق در معرض نور خورشید هستند. از ویژگی های استفاده از مستربچ مقاوم به یو وی می توان به افزایش عمر مفید محصولات، حفظ رنگ و ظاهر اولیه، مقاومت در برابر خوردگی و کاهش هزینه های نگهداری اشاره کرد. مهم ترین کاربر های مستربچ آنتی یو وی عبارتند از:
تولید قطعات خودرو : برای جلوگیری از تغییر رنگ و شکنندگی قطعات پلاستیکی داخلی خودرو از افزودنی آنتی یو وی در تولید آن ها استفاده می شود. دستگیره و کنسول خودرو در معرض تابش نور مستقیم خورشید هستند به همین ترتیب برای تولید آن ها از افزودنی آنتی یو وی استفاده می شود. از جمله قطعات بیرونی خودرو که با استفاده از مستربچ افزودنی آنتی یو وی تولید می شوند می توان به چراغ های خودرو اشاره کرد. سقف و پانل های بیرونی، روکش و پوشش ها و قطعات پلاستیکی نمای بیرونی خودرو با استفاده از این مستربچ تولید می شوند.
مستربچ ضد اکسیداسیون
به منظور جلوگیری از اکسیداسیون و آسیبهای ناشی از آن به مواد پلاستیکی در هنگام فرآیند تولید و استفاده، به ترکیب پلاستیکها اضافه میشود.مستربچ ضد اکسیداسیون میتواند از تغییر رنگ پلاستیکها به دلیل اکسیداسیون جلوگیری کند، که این ویژگی برای حفظ کیفیت ظاهری محصولات بسیار مهم است.این مستربچ به کاهش آسیبهای ناشی از رادیکالهای آزاد و تأثیرات منفی محیط زیست کمک کرده و باعث افزایش عمر مفید محصولات پلاستیکی میشود. اکسیداسیون معمولاً بهویژه در دماهای بالا بیشتر رخ میدهد. مستربچ ضد اکسیداسیون میتواند در این شرایط مقاومت پلاستیک را افزایش دهد. این نوع مستربچ بهویژه در فرآیندهایی مثل اکستروژن یا تزریق پلاستیک کمک میکند تا کیفیت مواد تولیدی حفظ شود و از ایجاد مشکلاتی چون گسیختگی و تردی جلوگیری کند.مستربچ ضد اکسیداسیون معمولاً با انواع مختلف پلیمرها مانند PE، PP، PVC، و دیگر مواد پلاستیکی سازگاری دارد و میتوان آن را به راحتی در فرآیند تولید بهکار برد.استفاده از مستربچ ضد اکسیداسیون میتواند به طور چشمگیری کیفیت و عمر محصولات پلاستیکی را در برابر شرایط محیطی مختلف بهبود بخشد.
مستربچ ضد الکتریسیته ساکن
مستربچ ضد الکتریسیته ساکن برای کاهش ایجاد الکتریسیته ساکن استفاده می شود. این مستربچ معمولا از ترکیب مواد ضد الکتریسیته ساکن و پلیمر ها ساخته می شود. بیشتر لوازم خانگی، بسته بندی های الکترونیکی، وسایل صنعتی حساس به الکتریسیته ساکن با استفاده از این مستربچ افزودنی ساخته می شوند. مستربچهای ضد الکتریسیته ساکن میتوانند از جمع شدن بار الکتریکی روی سطح پلاستیک جلوگیری کنند.این مستربچها به گونهای طراحی میشوند که هدایت الکتریکی سطح را افزایش دهند، به طوری که بار الکتریکی به راحتی از سطح پلاستیک تخلیه شود. این مستربچها را میتوان به انواع پلاستیکها از جمله پلیاتیلن، پلیپروپیلن، پلیاستر و دیگر پلیمرها اضافه کرد. این نوع مستربچها پایدار هستند و میتوانند برای مدت طولانی ویژگیهای ضد الکتریسیته ساکن خود را حفظ کنند.با جلوگیری از آسیبهای ناشی از الکتریسیته ساکن، این مستربچها میتوانند عمر مفید محصولات پلاستیکی را افزایش دهند.
مستربچ مقاوم به شعله
شامل افزودنیهای مقاوم به شعله برای کاهش اشتعالپذیری پلیمرها می شود. از مستربچ مقاوم به شعله در صنایع خودروسازی، ساختمانی و الکترونیکی استفاده می شود. مستربچ مقاوم به شعله نوعی افزودنی شتاب دهنده های فرایند است که برای افزایش مقاومت پلیمرها در برابر اشتعال و کاهش خطر آتشسوزی استفاده میشود. این مستربچ حاوی ترکیباتی است که خواص ضد شعله به مواد پلاستیکی میدهد و فرآیند اشتعالپذیری را کند یا متوقف میکند. سایر ویژگی های مستربچ مقاوم به شعله عبارتنداز :
پایداری در دماهای بالا: این مستربچها به پلیمرها کمک میکنند تا در دماهای بالا بدون تجزیه یا اشتعال پایدار بمانند.
سازگاری با انواع پلیمرها: مستربچهای مقاوم به شعله میتوانند با بسیاری از مواد پلاستیکی مختلف از جمله پلیاتیلن، پلیپروپیلن، ABS، و PVC سازگار باشند.
کاهش تولید دود: برخی از انواع مستربچهای مقاوم به شعله به گونهای طراحی شدهاند که میزان دود و گازهای سمی تولیدشده در هنگام آتشسوزی را کاهش دهند.
کاهش اشتعالپذیری: مستربچ مقاوم به شعله با ایجاد یک لایه محافظ بر روی سطح مواد پلیمری، از گسترش شعله جلوگیری کرده و سرعت احتراق را کاهش میدهد. مستربچ مقاوم به شعله باعث کاهش سرعت اشتعال و جلوگیری از انتشار شعله در محصولات پلاستیکی میشود. برخی از انواع این مستربچها دود و گازهای مضر کمتری تولید میکنند و به این ترتیب خطرات سلامتی و زیستمحیطی را کاهش میدهند. این مستربچ میتواند با بسیاری از پلیمرها مانند پلیاتیلن، پلیپروپیلن، PVC، و ABS سازگار باشد.
روش استفاده از افزودنی در تولید محصولات پلیمری
برای استفاده از افزودنی شتاب دهنده های فرایند باید به نکاتی توجه کرد برای مثال توجه به مقدار دقیق افزودنی ها اهمیت بسیاری دارد. نگهداری از مستربچ های افزودنی نیاز به نگهداری صحیح دارد برای مثال مستربچ ها را باید دور از رطوبت نگهداری کرد و نباید در محیطی قرار بگیرند که حرارت بسیار بالا است. نگهداری مناسب از مستربچ ها باعث می شود که خواص آن ها حفظ شود. قبل از تولید انبوه نیاز است که مخلوط نهایی مورد آزمایش و بررسی قرار بگیرد و ارزیابی شود. ارزیابی مواد بدست آمده باعث می شود که محصولات تولید شده از کیفیت بالایی برخوردار باشند.
استانداردها: باید به استانداردهای بینالمللی یا ملی مربوط به مصرف افزودنیها پایبند بود تا ایمنی و کیفیت محصول تضمین شود.
نوع پلیمر: افزودنی باید با نوع پلیمر مورد استفاده سازگار باشد. برای مثال، برخی افزودنیها برای پلیاتیلن مناسب هستند اما ممکن است با پلیپروپیلن یا PVC کارایی نداشته باشند.
کاربرد نهایی محصول: انتخاب افزودنی شتاب دهنده های فرایند باید بر اساس کاربرد نهایی محصول باشد. برای مثال، اگر محصول در معرض نور خورشید قرار میگیرد، افزودنی مقاوم به UV ضروری است، در حالی که در محصولات بهداشتی، افزودنیهای ضد باکتریایی ممکن است مورد نیاز باشند.
مقدار مناسب: مصرف بیش از حد یا کم افزودنی میتواند بر کیفیت نهایی محصول تأثیر منفی بگذارد. مصرف بیش از حد ممکن است منجر به تغییر در ویژگیهای مکانیکی و شیمیایی پلیمر شود، در حالی که مصرف کمتر از حد مورد نیاز نمیتواند خواص مطلوب را ایجاد کند.
توزیع یکنواخت افزودنی: افزودنی شتاب دهنده های فرایند باید بهطور یکنواخت در سراسر پلیمر توزیع شوند تا تمامی بخشهای محصول از خواص مطلوب بهرهمند شوند. عدم توزیع مناسب میتواند باعث ایجاد نقاط ضعیف در محصول نهایی شود.
سازگاری افزودنیها با یکدیگر: در صورتی که از چند نوع افزودنی بهصورت همزمان استفاده میشود، باید از سازگاری آنها با یکدیگر اطمینان حاصل کرد. برخی افزودنیها ممکن است واکنشهای ناخواستهای با هم داشته باشند و عملکرد یکدیگر را مختل کنند.
پایداری حرارتی افزودنیها: برخی افزودنیها در دماهای بالا پایداری ندارند و ممکن است در طی فرآیند تولید (مانند اکستروژن یا قالبگیری تزریقی) تجزیه شوند. بنابراین، باید افزودنیهایی انتخاب شوند که پایداری حرارتی مناسب برای فرآیند تولید داشته باشند.
تأثیر بر ویژگیهای مکانیکی محصول: برخی افزودنیها ممکن است باعث تغییرات در ویژگیهای مکانیکی پلیمر مانند استحکام کششی، انعطافپذیری یا سختی شوند. باید افزودنیها به گونهای انتخاب شوند که این ویژگیها بهبود یابند یا در صورت نیاز تغییر کنند.
تأثیر بر زمان فرآیند تولید: افزودنیها ممکن است زمان فرآیندهایی مانند سرد شدن یا تنظیم قالبگیری را تغییر دهند. برای جلوگیری از تأخیر در تولید، لازم است که تأثیر این افزودنی شتاب دهنده های فرایندبر زمان فرآیند تولید مورد ارزیابی قرار گیرد.
از ویژگی و مزایای استفاده از مستربچ افزودنی می توان به بهبود خواص فیزیکی، شیمیایی و عملکردی پلیمر ها که سبب بهینه سازی عملکرد محصول نهایی می شوند اشاره کرد. ترکیب مستربچ افزدنی با مواد پلیمری سبب کاهش هزینه های تولید و بهینه سازی مصرف مواد اولیه، بهبود کیفیت و کارایی فرایند تولید پلاستیک و .. می توان اشاره کرد. برای بهبود مقاومت محصولات در برابر شرایط محیطی مختلف نور، گرما، مواد شیمیای و .. از مستربچ افزودنی استفاده می شود.
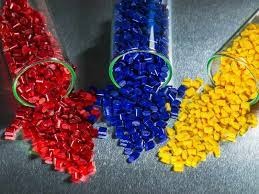
نحوه استفاده از افزودنی در صنایع پلاستیک
افزودنیها نقش بسیار مهمی در بهبود و تطبیق ویژگیهای محصولات با نیازهای خاص دارند و کاربردهای گستردهای در صنایع مختلف دارند. اضافه کردن افزودنیها به صورت مستربچ به جای استفاده از مواد خام به صورت جداگانه، هزینههای تولید را کاهش میدهد. مستربچها امکان کنترل دقیقتر و یکنواختی بهتر در خصوصیات نهایی محصولات را فراهم میکنند. استفاده از مستربچها میتواند زمان تولید را کاهش داده و بازدهی فرآیند تولید را افزایش دهد. نحوه استفاده از افزودنی ها بر اساس نیاز های خاص هر محصول متفاوت خواهد بود. برای افزایش ویژگی های محصولات پلاستیکی نیاز است که افزودنی ها را به مقدار مشخصی با ماده پایه مخلوط شوند. پس از مخلوط کردن مواد افزودنی با پلیمر لازم است که مخلوط نهایی را به مرحله تولید انتقال داد. در نهایت محصولات تولید شده باید آزمایش شوند تا از کیفیت و تطابق با مشخصات مورد نظر اطمینان حاصل شود. مراحل استفاده از مستربچ افزودنی به طور کلی به صورت زیر است:
انتخاب مستربچ مناسب:بر اساس نیازهای خاص محصول نهایی و نوع پلیمر پایه، مستربچ مناسب انتخاب میشود. به عنوان مثال، اگر نیاز به مقاومسازی در برابر اشعه UV باشد، از مستربچهای ضد UV استفاده میشود.
توزیع و آمادهسازی:مقدار مشخصی از مستربچ و پلیمر پایه باید دقیقاً وزنکشی و آماده شود. نسبت مستربچ به پلیمر پایه بر اساس توصیههای تولیدکننده مستربچ و نیازهای محصول تنظیم میشود.
اختلاط اولیه:مستربچ و پلیمر پایه به صورت اولیه مخلوط میشوند. این مرحله ممکن است با دست یا با استفاده از تجهیزات خاصی مانند میکسرهای مکانیکی انجام شود تا اختلاط اولیه به صورت یکنواخت صورت گیرد.
فرآیند اکستروژن:مخلوط مستربچ و پلیمر پایه وارد اکسترودر میشود. در این مرحله، مواد تحت حرارت و فشار مناسب قرار گرفته و به صورت یکنواخت با یکدیگر ترکیب میشوند. دما و فشار در این مرحله باید دقیقاً کنترل شود تا اختلاط کامل و یکنواخت صورت گیرد.
خنکسازی و گرانولسازی: پس از اختلاط کامل، مواد مذاب از اکسترودر خارج شده و خنک میشوند. سپس به صورت گرانولهایی (حبوبات پلاستیکی) برش داده میشوند تا آماده استفاده در مراحل بعدی تولید باشند.
تزریق یا فرآیندهای دیگر تولید:گرانولهای تولید شده در فرآیندهای مختلف تولیدی مانند تزریق پلاستیک، بادیمولدینگ، اکستروژن فیلم و … استفاده میشوند تا محصولات نهایی با ویژگیهای مورد نظر تولید شوند.
کنترل کیفیت:محصولات نهایی باید از نظر کیفیت و ویژگیهای فیزیکی و شیمیایی کنترل شوند تا اطمینان حاصل شود که افزودنیها به درستی عمل کرده و محصول نهایی دارای ویژگیهای مورد نظر است.
کاربرد های مستربچ افزودنی
مستربچ افزودنی (Additive Masterbatch) ترکیبی است که شامل یک یا چند ماده افزودنی بوده و بهصورت کنسانتره در یک پایه پلیمری (معمولاً یک نوع پلاستیک) تولید میشود. این مستربچها به پلاستیکها اضافه میشوند تا خواص یا ویژگیهای خاصی به مواد پلاستیکی بدهند.مستربچ افزودنی به دلیل ترکیب یکنواخت با پلیمر پایه، خواص افزودنی را بهصورت همگن در سراسر محصول توزیع میکند و از عدم یکنواختی در ویژگیهای محصول جلوگیری میکند.مستربچهای افزودنی میتوانند مقاومت مکانیکی مانند سختی، انعطافپذیری و استحکام کششی مواد پلیمری را بهبود بخشند. همچنین در برابر مواد شیمیایی مانند اسیدها و بازها مقاومت ایجاد میکنند. کاربرد های مستربچ افزودنی عبارتند از :
افزودنیهای رنگی: برای افزودن رنگهای مختلف به محصولات پلاستیکی
آنتیاستاتیک: برای کاهش تجمع الکتریسیته ساکن در محصولات پلاستیکی
مقاومت در برابر شعله: افزودنیهایی که به پلاستیکها اضافه میشوند تا آنها را در برابر آتش مقاوم کنند.
ضد اکسیداسیون: مستربچهایی که برای جلوگیری از اکسیداسیون و کاهش سرعت فرسودگی مواد پلاستیکی استفاده میشوند.
پایداری در برابر اشعه UV: به مواد پلیمری افزوده میشود تا مقاومت آنها در برابر تخریب ناشی از نور خورشید و اشعه ماوراء بنفش افزایش یابد.